- Overview
- Product Description
- Chart
- Product Parameters
- Company Profile
- FAQ
Basic Info.
Product Description
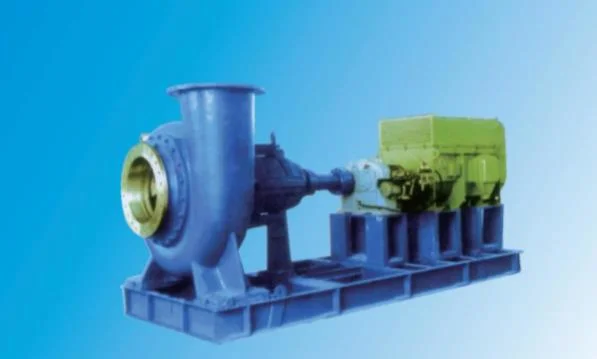
Flow range: 4~12000m3/h
Lift range: ~100m
Design pressure: 2.5MPa at most Application temperature: -40~180ºC
Application field: transport particle contained wear-resisting and anti-corrosive slurry. Mainly used in environmental protection industry for the delivery or circle of various desulfurization, denitration process circulating slurry, or used for the delivery of other wear-resisting, anti-corrosive slurry.
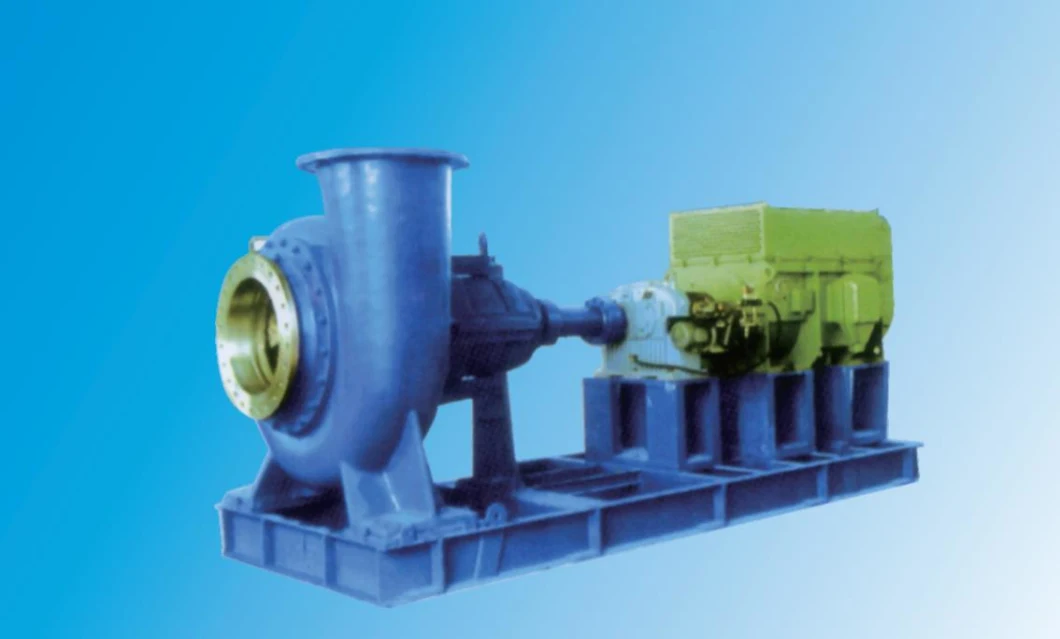
Product overview
F-TL desulfurization pump is a new generation high-efficient desulfurization pump based on the successful design experience of ZM series slurry pump. It absorbs domestic and foreign advanced technology of the same type products and is designed aimed at flue gas desulfurization pump properties in our country. Its maximum flow range reaches 12000m3/h. Its lift is normally below 100m, covering all desulfurization system pump working conditions. It can be used as absorbing tower large-scale slurry circulating pump or limestone slurry transporting pump, gypsum slurry discharge pump, recovery pump and pit pump etc.
Structure
FT-L type applies horizontal, single pump shell, single-stage single-suction, bracket(suspension) type structure. It applies flexible coupling.
Slurry PH: 2.5~13
Chloride ion concentration:≤60000ppm
Weight concentration:≤60%
Medium temperature:≤120ºC
Performance and material characteristics
Hydraulic design applies computer CAD assisted design and 2-phase flow theory design High efficiency, long service life, reliable operation.
Transflux parts apply all-metal anti-corrosive Cr-Ni alloy materials, both wear resisting and corrosion resisting. Surface intergranular gap is small. It has good chloride resistant stress corrosion cracking capability and better mechanical strength High operation reliability. All-metal pump overcomes problems of non-metal liner which has defects of falling, tearing and deforming.
Hydraulic friction loss is small. Efficiency is 3% higher than non-metal pump of the same parameter.
All-metal pump dimension is easy to control. Component surface finish is high and component fit clearance is small. Volumetric efficiency is high. Comprehensive efficiency is 5% higher than non-metal pump.
Transflux parts have a long service life. Metal backplate has a better resistance to shear sliding wear than normal non-metal materials. It can bear long time of shear wear.
Dynamic wear resistance is 0.008-0.08mm/year. Tensile strength is high. Keep a stable performance under long abrasion working cond ions.
Shaft sealing type
Shaft sealing all applies mechanical seal. Our company mechanical seal is divided into shaft sealing water type and no shaft sealing water type.
Shaft sealing water type
Combined mechanical sealing. Shaft sealing water flow is 0.1~1% of pump flow, but no less than 1m3/h at least. Shaft sealing water pressure is 1/2 of pump outlet pressure.
No shaft sealing water type
Anhydrous medium self-flushing type mechanical sealing, unique structure, good water conservation effect.
Model instruction

1 | Before the pump cover | 2 | Impeller nut | 3 | Chuck | 4 | Before the liner | 5 | Pump body | 6 | Impeller |
7 | After the pump cover | 8 | Mechanical seal | 9 | Before the dust disk | 10 | Front axle bearing cover | 11 | Shaft | 12 | Bearing box |
13 | Rear axle beaing cover | 14 | Ater the dust-prod plate | 15 | Bearing box bracket |
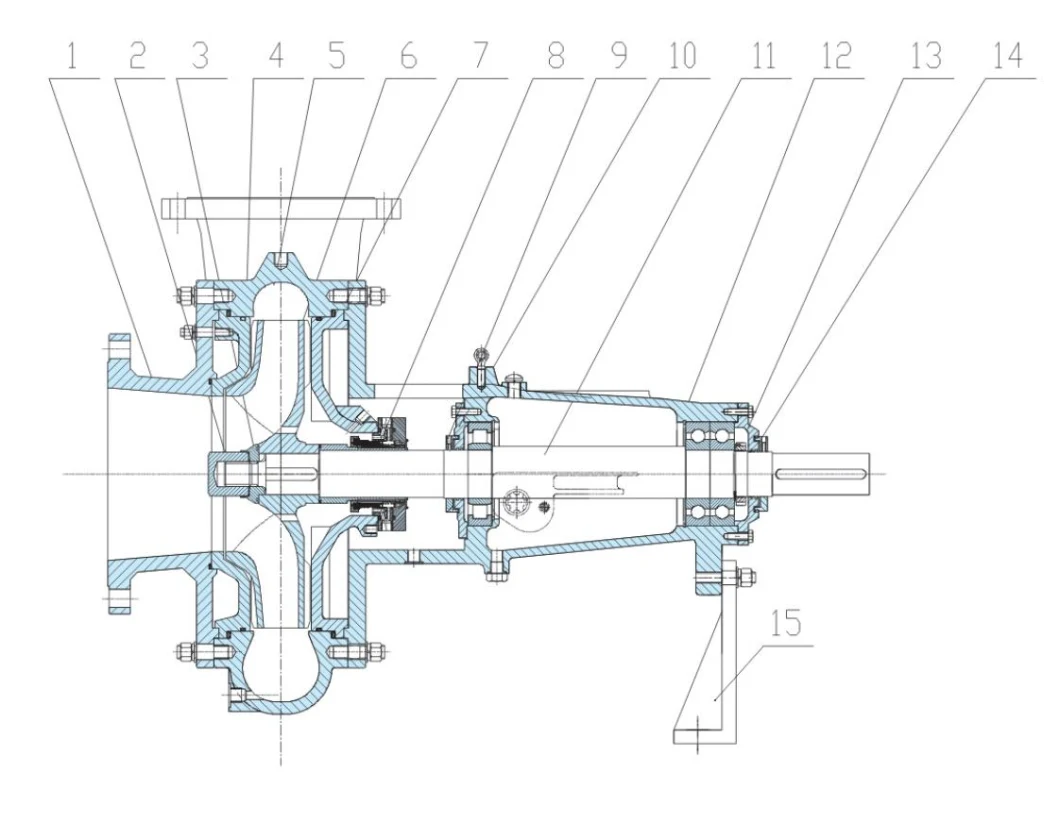
1 | Before the pump cover | 2 | Impeller nut | 3 | Chuck | 4 | Before the liner | 5 | Pump body | 6 | Impeller |
7 | After the pump cover | 8 | Mechanical seal | 9 | Before the dust disk | 10 | Front axle bearing cover | 11 | Shaft | 12 | Bearing box |
13 | Rear axle beaing cover | 14 | Ater the dust-prod plate | 15 | Bearing box bracket |
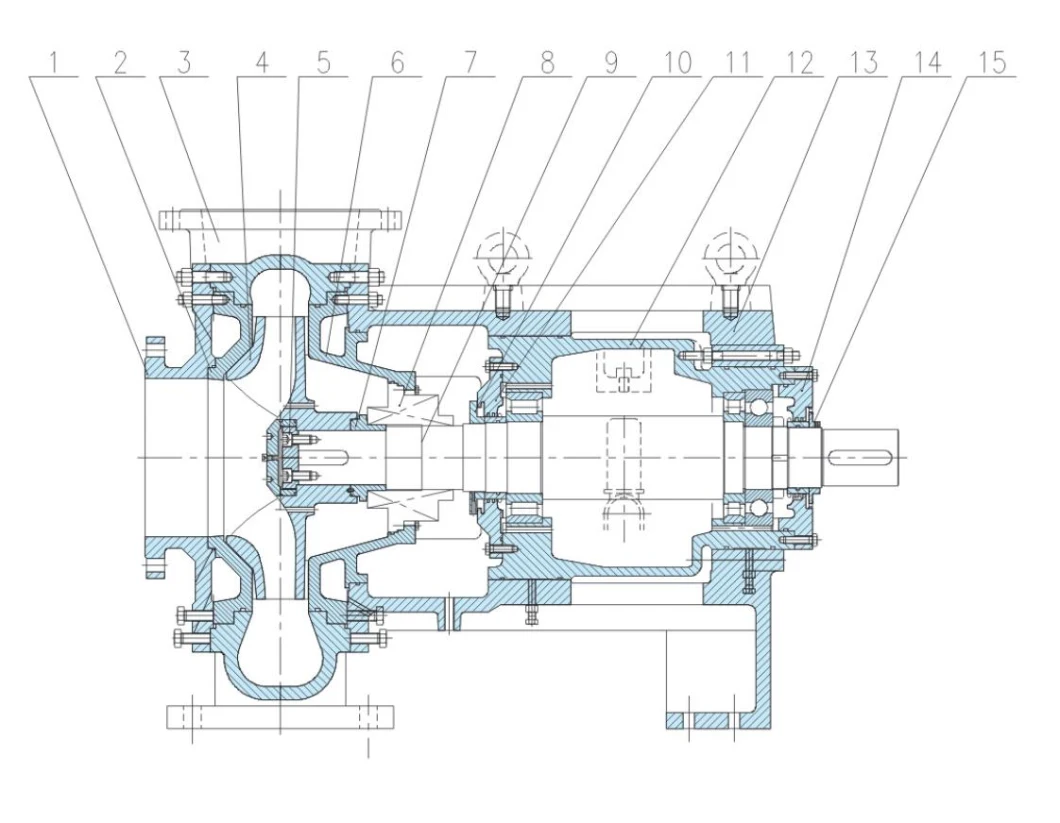
1 | Before the pump cover | 2 | Before the liner | 3 | Pump body | 4 | Impeller | 5 | Impeller nul component | 6 | After the pump cover |
7 | Machine sealing collar | 8 | Mechanical seal | 9 | Shaft | 10 | Before the dust disk | 11 | Front axle bearing cover | 12 | Bearing box |
13 | Bearing box brackel | 14 | Rear axle bearing cover | 15 | Ater the dust-prool plate |
Performance parameters of the table
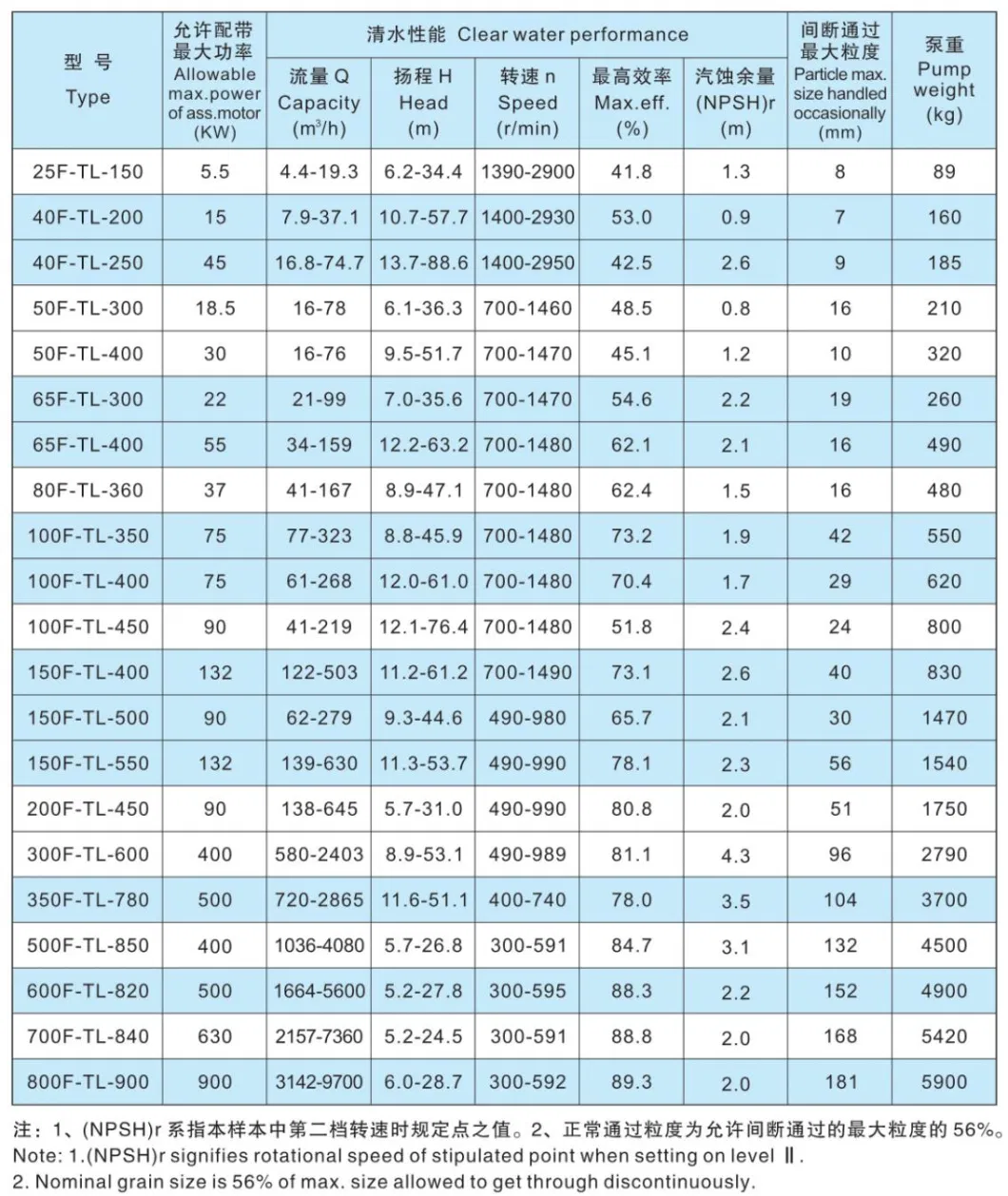